Isn’t that a soup? you think to yourself as you overhear “bisque” in your local pottery studio.
But you’ve heard it enough to know it’s a part of pottery, so you’ve gone to look it up. Lucky for you, we’ve written this article to define what bisque ceramics are and what role they play in making pottery.
What is bisque pottery?
Bisque or bisqueware is one of the 7 stage of clay. Bisque firing is a low-fire event. During this firing, bisque clay becomes durable creating bisque pottery.
Let’s start with definitions: Ceramics is Greek. It means “for pottery” or “of pottery” (Fitting!). Bisque has a French origin meaning “twice-baked” or “twice-cooked”. We’re talking about pottery, so we care about the baking definition.
Bisque fired pottery is typically not the final stage. bisque fired clay is porous meaning it absorbs water. A porous vessel can’t be used to hold liquids. Once bisque fired, a potter will typically glaze, paint, or decorate a pot. Then, the pot is fired again at higher temperatures.
The term “Bisque” is used a lot in ceramics and in different ways. Here are the three main ways you’ll hear the term used and what it means:
- Bisque firing: This is the process leading to the actual bisqueware. More on this below.
- Bisque: This is a clay vessel that has been fired once and is now durable. Bisque also refers to a porous state which is great for glazing. If glazed, a potter then fires the bisqueware again. This is when the vessel is officially at the glazeware stage of clay. Once glazeware, the piece can be used for liquids (think coffee mugs or bowls).
- Bisqueware: This is the state a vessel is in after being bisque fired. It’s sometimes referred to as “biscuit ware” or “biscuit porcelain”. The difference between “bisqueware” and “bisque” is that a bisqueware piece will remain in the bisqueware form.
Bonus: Bisque porcelain
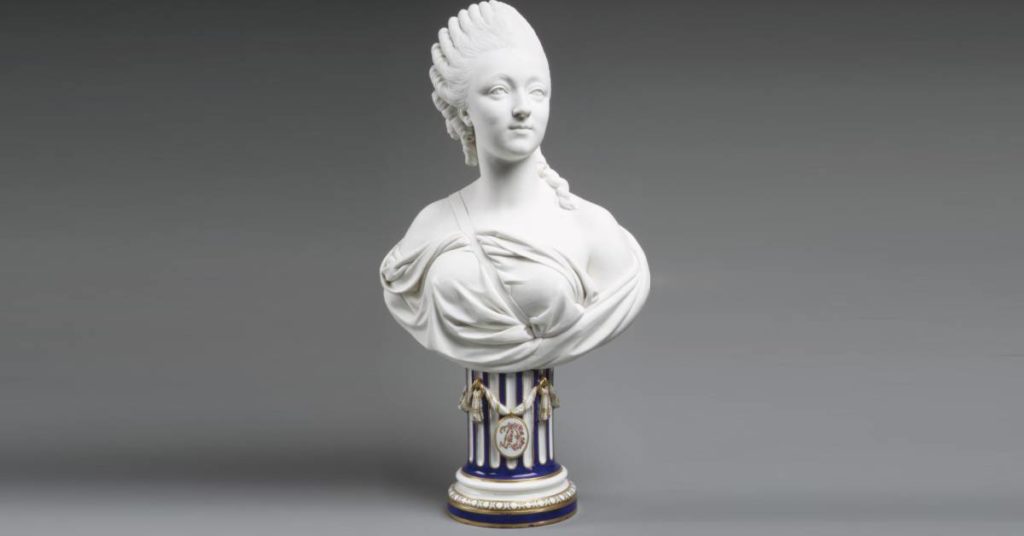
You’ll hear about this less in traditional day-to-day pottery. It’s less functional and so less used.
But bisque porcelain (or China clay) is a popular finished style in Europe. When porcelain is bisque fired, it takes on a smooth appearance. I’ve seen it used for sculptures and busts because of the similarities to a marble finish.
Bisque firing
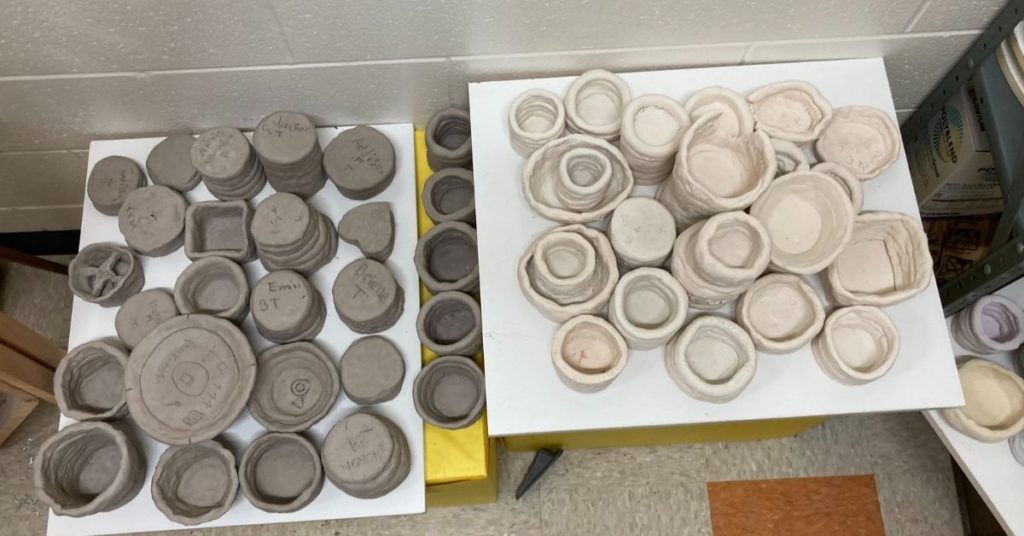
The bisque stage is a key part of most ceramic processes and is the first firing a ceramic ware goes through. The goal of bisque firing is multi-layered.
First, it changes the nature of clay and becomes a ceramic. It holds its shape and is porous. Plus, it’s ready for glazing. Ceramic glazes need a porous surface to be able to soak into the entire piece.
Second, bisque firing removes any remaining water preparing the pot for extreme heat in the final firing. One of the primary reasons for clay cracking is uneven firing and uneven drying. Bisque firing happens at a low-fire temperature. Moisture is removed and a lower grade of stress on the vessel.
Third, bisque firing helps ceramic glazes and ceramic paints bind to the ceramic material.
Bisque firing temperature
Bisque firing is typically done at a low-fire temperature.
The “low” firing range is most commonly used in bisque firing, but can also be used in firing some glazes. The pyrometric cones for low-firing are 010 to 02. That’s a cone temperature of between 1636° – 2052° Fahrenheit. Low fire in pottery is high temperatures for the rest of us!
The lower temperature (cones 010 – 08), allows ceramic pieces to be more porous. This is best for items you want to glaze. On the higher end (cones 07 – 04), your wares will become more durable, but less porous.
If you’re not sure what cones are, be sure to read our article “what does cone mean in ceramics?“
How long does it take to bisque fire?
It takes about 10 to 12 hours for bisque firing. During those 10-ish hours, the clay particles go through chemical changes that makes it bisqueware.
It’s important to keep a firing schedule when bisque firing. Else you may lose all your hard work to a kiln explosion. The bisque firing process is variable based on the type of kiln you use. Most commonly you’ll use either a gas or electric kiln. And if you’re using a modern kiln, it’s more a “set and forget” situation.
The following are a general outline for each firing stage are:
- Slowly warm up the kiln. Turn on the kiln to raise the temperature. Your pot should be in the bone dry stage and is NOT in the kiln while it warms up.
- Two – three hours at low heat. Once the kilns warmed up, place your wares in the kiln. The kiln should slowly heat up for about two hours.
- Two – three hours at medium heat. Nothing to do here if your kiln is programmatic. You can peak in your ceramics if you have a window. Your ware should be at medium heat for another two hours.
- Two – three hours at a higher temperature. This is not to be confused with “high-fire” which are commercial level temperatures. It’s instead a measurement of how quickly the kiln heats up. Again, the vessels should be in the kiln for about 2 hours.
It’s a good idea to use polymetric cones or witness cones when you’re working with a kiln. They can help you stay on target while waiting a long time for the pieces to finish.
The last step is to let the kiln cool down with the wares inside. After the kiln is cool, open the door and let it cool with room temperature air flowing in for a few more hours before removing your now bisque fired vessels.
Shrinkage during bisque firing
At any stage after the plastic stage of clay, your vessels will shrink. There’s no getting around it. But as far as bisque firing goes, your pots shouldn’t shrink all too much. If they do, they are likely to crack. That’s why it’s so important they are in the bone dry stage of clay before putting them in the kiln. Otherwise, the wares may shrink rapidly putting a lot of stress on the vessel.
Glazing bisque and other decorations
Once bisque firing is done, most potters will glaze, decorate, or paint the pot.
You’ve heard it many times in this post, but a bisque pot is an incredibly porous vessel. That means glazes, paints, and other decorations adhere well to the clay surface. The best type of paint to use is acrylic paint. The best type of glaze is determined by the color and finish you’ll want with the piece.
This is also a necessary step if you want to use your ceramic work in to hold liquids. A porous clay body will absorb whatever liquids you put in the container. Glazing bisque and glaze firing make your pot ready to use.
Note: Not all glazes are food-safe. Be sure to research your glaze before using it on a piece intended for the kitchen.
Conclusion
Ceramic bisque is a necessary stage of clay that gets your work one step closer to being used in everyday life. It takes your bone dry pot and makes it durable.
If you have any questions or think we missed an important step, please let us know! Leave a comment or contact us directly at hello@wheelandclay.com.
Related articles
Did you enjoy learning about bisqueware and how it fits into the overall discipline of making ceramics? Good news! We have more articles like this on our blog. Check them out at the links below.