Did you see the episode of The Great Pottery Throw Down where they did raku pottery? Yeah, I loved that one, too. And if you haven’t seen it, I have a clip down below. It’s worth checking out.
Now that you’ve been inspired, I’m sure you’re wondering what raku pottery is and how you could make it. Well, you’ve come to the right place. In this article, we’ll share history, how to make it, and combustible materials to use.
Let’s get to it 👇
What is raku pottery?
Raku pottery is a firing method in ceramics. A potter removes a clay body from a kiln at high temperatures causing it to cool quickly. As it cools, the potter applies combustible materials like paper or horsehair. The resulting designs are rich, textured, and unique.
History of raku ceramics
Raku ware is a popular type of Japanese pottery. The art form was started in the 16th century by a tea master named Sen no Rikyū and quickly became a common part of Japanese society. The name “raku” comes from a Chinese symbol that means enjoyment. Over time, “Raku” became the family name for those most known for making raku ware.
Early Japanese raku ware made by the Raku family was traditionally handbuilt through the pinch pot technique. The invention and adoption potter’s wheel made making vessels easier. But many raku artists continue handbuilding their wares because of the deep connection raku, tea ceremonies, and all of Japanese culture has to Zen philosophy. With respect to Zen traditions, coloring and decoration were neutral and muted. Modern potters who continue the raku tradition have since experimented with bright colors.
Japanese tea ceremonies and raku ware
Tea ceremonies in Japan are a way of preparing and drinking tea with a focus on hospitality to guests. The ceremonies are a deeply rooted part of Japanese culture. The ceremony encourages a slowing of pace from everyday life and is connected to Zen philosophy.
Raku ware is intertwined with tea ceremonies. As we explored earlier in the article, raku tea bowls were the result of a prominent tea master and tea masters make raku pots a core component of the tea ceremony. Japanese raku pottery forms are modest. The unadorned pieces fit well in the Zen way of life.
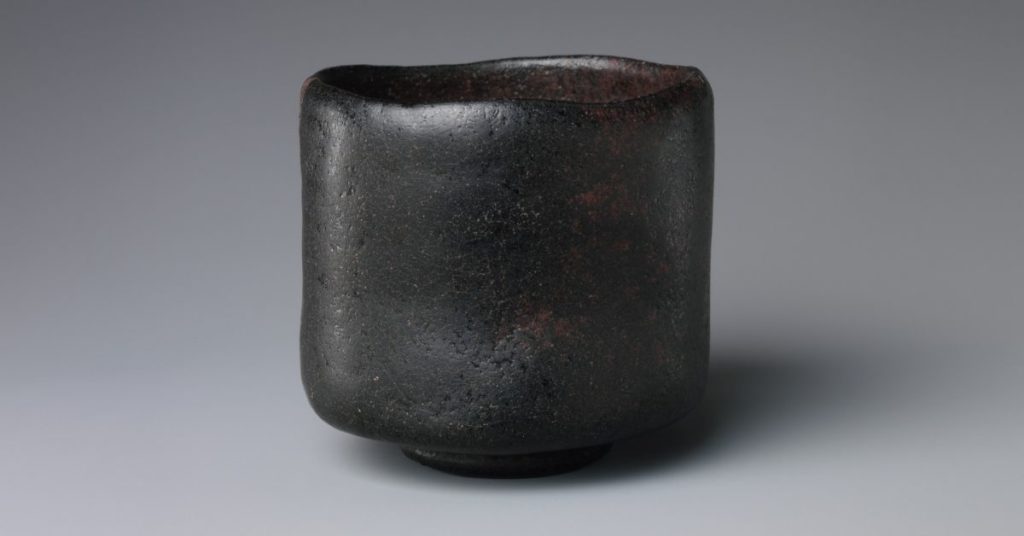
Western raku ware
The Japanese tradition of raku ceramics spread to the west in the early 1900s by Bernard Leach. Leach traveled to Tokyo where he was introduced to the raku firing technique. He returned home bringing with him the concept. Decades later, Paul Soldner popularized the tradition for American ceramicists.
The western raku technique and Japanese raku style differ in two ways.
- Japanese raku ceramics are typically brown glaze, black glaze, or red glaze resulting in neutral tones. Western raku pottery uses bright colors and is often playful.
- Japanese raku-fired pottery is part of the Japanese tea ceremony, a Zen practice. Raku firing in the west is an experimental method of firing. The cultures change the outcomes of raku pieces.
Here’s a western raku ceramic piece from Bernard Leach. Note the vibrant colors of the American raku compared to the muted, solemn work normally seen in Japanese ceramics.
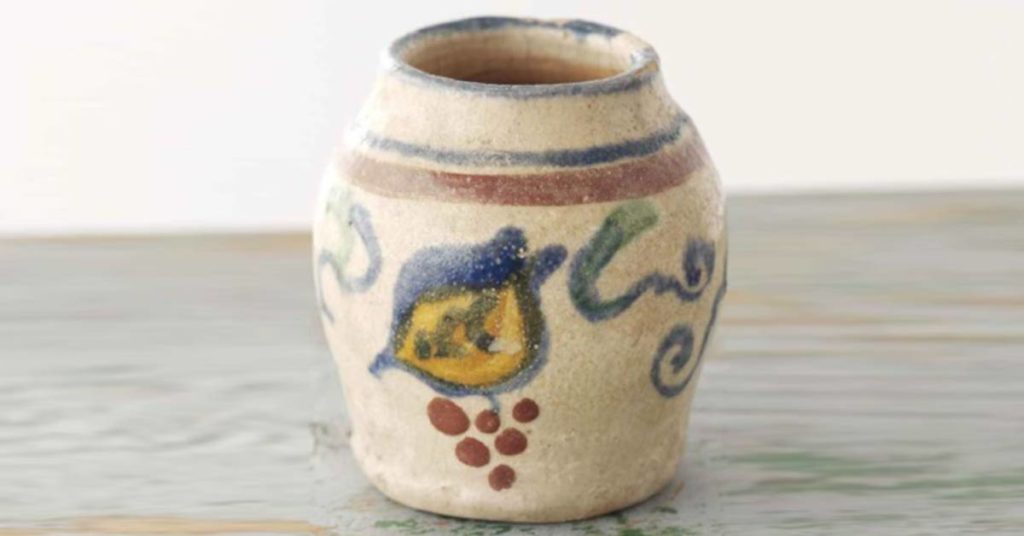
How to make raku pottery
What type of clay is best?
The traditional Japanese raku process typically uses stoneware. Stoneware is a less porous and sturdier material than its porcelain and earthenware siblings. It’s also incredibly durable. The durability aspect can withstand the dramatic heat changes that come along with doing the raku firing method.
It’s wise to include what we refer to as “opening agents” in the biz.
Exposure to thermal shock is inevitable in the Raku process. An opening agent reduces the amount of expanding and contracting a clay body goes through reducing the stress on the vessel. The added opening agent helps to withstand sudden thermal shocks without the vessel cracking. Raku clay should have some opening agents mixed into them like sand and grog.
Also, bisque firing before raku fired can open up a clay body. The clay is less dense once bisque fired. This protects it against damage during extreme temperature changes of raku firing.
Raku firing process
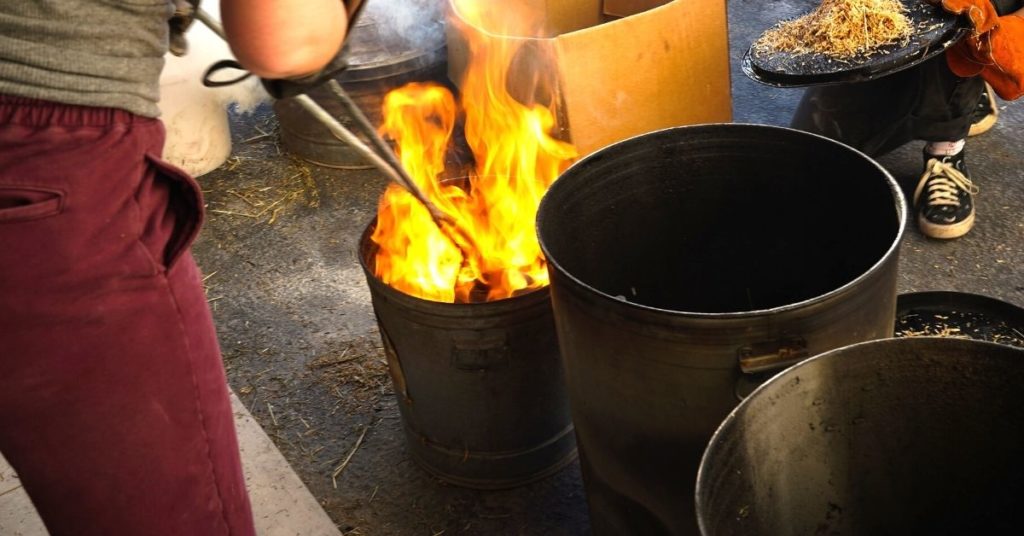
Raku pottery firing is the crux of the technique. It’s probably the most exhilarating part of the whole process! I get both excited and terrified when I do it. The process is considered a low temperature firing because of the open-air setup.
First, start by loading the kiln and turning it on. The internal temperature will rise to around 1800°F. With a small kiln (recommended), the temperature will reach the desired range quickly. This should take an hour or less.
Keep an eye on the pots. Turn off the burners once the surface of the vessels is smooth. Open the kiln right away. The interior will be incandescent.
Safety precautions: I’m not your mom, but it’s important 🙂 Wear gloves, goggles, and work.
Remove the pottery with tongs. Quickly, but steady eddy with it! Pop the pot in a post-firing combustion chamber with whatever combustible material you’re using. You can see more about combustible materials that are commonly used and that we recommend further down the page.
Raku Kilns
First, consider how the kiln will be unloaded. You’ll be removing your clay body when temperatures are high. So a smaller raku kiln is better than a larger one that you have to hunch over. Plus, we recommend a kiln with a side opening instead of a top-load kiln. A side kiln allows for easier maneuvering and puts you in less danger of getting burned.
For raku clay bodies, it’s best to use a gas or wood-fueled kiln. The firing process requires heating the clay body to high temperatures quickly. These fuel sources are better than others for rapid temperature change.
What about making your own? It’s not for everyone. But if you’re handy, there are a lot of resources online about how to make your own raku kiln that’s on your property.
Raku glazes
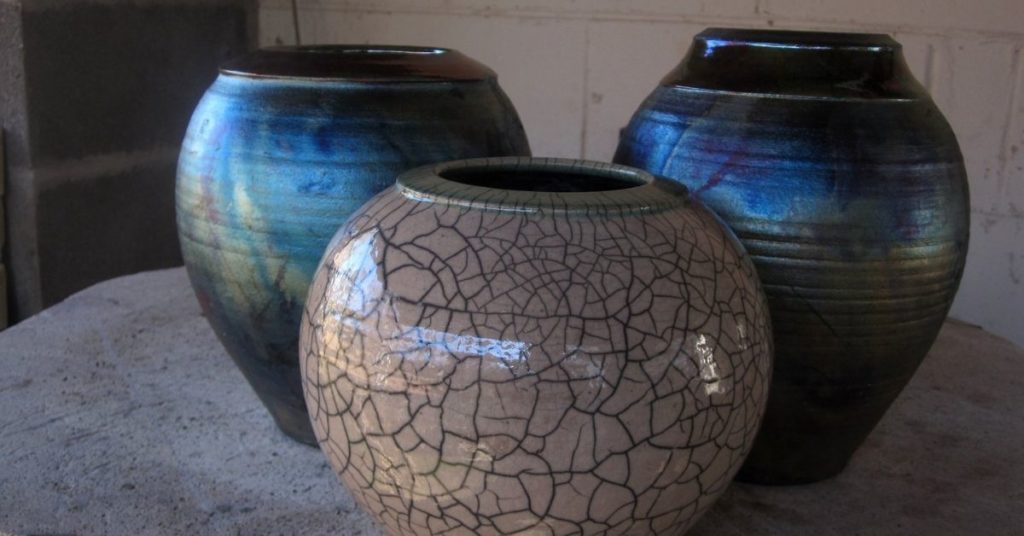
Raku glaze isn’t a specific type of glaze. Raku firing is in the low-fire range for kiln firing. So glazes made for low-fire firing will work. Think glazes made for cones ranging from 010 to 02.
The unique thing about raku and glaze is how a glaze reacts to the firing process. And experience with raku firing is the only way to best predict how a glaze will interact with the firing. It takes testing and trial to get the glaze surface right with raku pottery pieces. Have fun with experimenting!
You can make your own special glazes or buy commercially produced glazes. There are resources online with raku glaze recipes if you’re looking for instruction on making your own.
Combustible materials for raku firing
Combustible materials are introduced post-firing for decorative purposes. The natural materials often leave a unique design on the piece. Here’s a short list of combustible materials to get you started:
- Newspaper
- Horsehair
- Sawdust
- Straw
- Leaves
I promised to talk more about the amazing show, The Great Pottery Throw Down earlier in this blog… Here’s a really fun clip from the show showing the contestants doing the raku firing stage. You can see the organic material they choose to use and other things to style their pieces in the post-firing step.
Is Raku Pottery Food Safe?
Raku pottery is not food safe without proper sealing. This is because the quick-firing process leaves a ceramic piece fragile and porous.
A regular gas or electric kiln firing takes 8 – 12 hours to fire pottery properly. Raku firing is quick. Typically a raku piece is fired 30 – 90 minutes. Plus, firing raku happens at a much lower temperature. This low temperature and the short firing process doesn’t allow the clay body and glaze to mature leaving the clay porous (or susceptible to absorbing liquids).
Also, the rapid temperature change from pulling the hot pottery out of the kiln and into the open air often leaves a surface cracked or razed. Not a great feature for dinnerware!
There are ways of sealing raku pottery that make bowls and cups suitable for dinnerware and liquids.
Conclusion
Raku firing is a “hot” topic in the pottery world (ha!). And there’s no doubt why! The tradition is rich and the results are exquisite.
If you’re starting your own raku project, we’d love to hear how it goes! What worked for you? What didn’t work for you? What are you experimenting with? Simply send an email to hello@wheelandclay.com (include pictures – we love to see readers’ work!).
If have any questions or just want to say hi, leave a comment or email hello@wheelandclay.com. We’d love to chat.