So you’re ready to start your next project? Exciting! It’s always one of my favorite stages: Sketching, planning, picking out clay and glazes, and getting the grog content right…?
That last one doesn’t seem right, does it? Who thinks about grog?! Well, I do and in this article, we tell you everything you need to know about grog (and maybe even a little that you don’t need to know 🙂 ).
What is grog?
Grog is raw, granulated material that is added to clay to make the clay workable. Often grog is clay that has been fired and then ground up into a powder.
Grog in ceramics is typically either partially-fired bisque or full-fired vitrified ceramic that has been smashed up, ground up, and powdered. But there are grogs from raw materials like naturally occurring minerals like refractory rock.
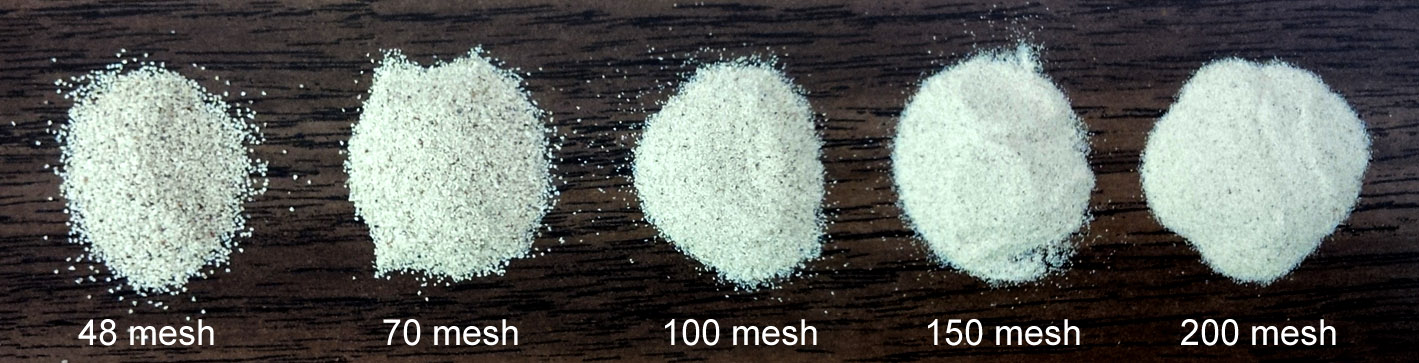
Grog has a practical feature in making your pottery more structurally sound. But it can also have an effect on the finish of a piece. This isn’t always a bad thing. Many finishes are quite lovely because of the textured finish grog causes.
How is ceramic grog made?
Why tell you when I could show you? Check out this fun video from Tony Soares Native Clays on YouTube.
Now, this is a pretty backyard version of making grog. As you can imagine, there are industrial-sized versions of this making grog with big machinery, silica sand, crystalline silica, and precision. But Tony’s video is cool and goes to show you it’s better to work with what you have than to stress about the perfect material.
The difference between soft and hard grog
Soft grog is a porous material. It’s called “soft” because it is fired at a lower temperature than the peak bisque firing temperature. It’s not usually used in the ceramic making because of its porous nature.
Hard grog has been fired at a higher temperature (over cone 10). Because it has gone through the full firing, its properties are more fitting for standard ceramic artwork.
What is the benefit of grog in clay?
The three main benefits of grog in clay are that it shrinks less, cracks less, and adds structure to your ceramic piece.
1. Grog means your piece shrinks less
The more grog you have in your clay, the slower the shrinkage rate during the drying process and when it fires because the clay body is less plastic with the particles included with grog.
2. Grog means your pieces crack less
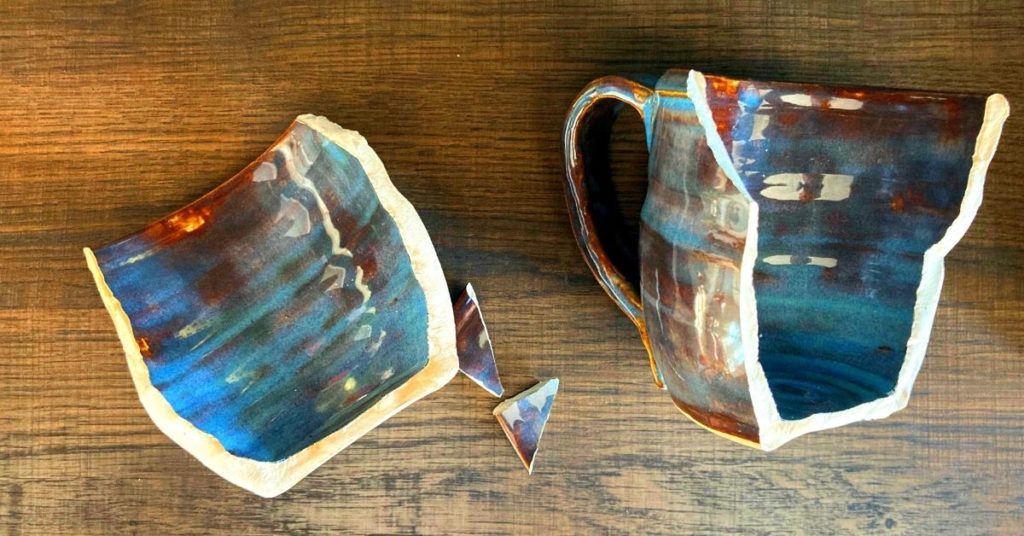
When clay shrinks, it puts pressure on the walls and structure of the piece. And when there’s pressure, a piece is more likely to crack.
This is especially true when you fire a piece. Firing at high temperatures places stress on the clay to harden it into your final ceramic work. The grog addition to a clay body slows the shrinking process and stabilizes the piece during that stressful period.
If you have more questions about why clay cracks you should visit our blog “6 causes of clay cracking in pottery“. We go into other reasons why your projects might be cracking like water content, room temperature, and the type of clay you’re using. Check it out!
3. Grog adds structure to your piece
Especially when building a larger pot. A piece can also have thinner walls and still maintain its structure when there is grog in the content of the clay.
The grog is like bricks. The rest of the clay is like mortar. The bricks hold the wall up while the mortar holds the bricks together.
How to tell how much grog is in a clay
The manufacturer’s label should share with you the grog contents. Locate the label and look for the line that has a percentage and then a measurement.
The percentage tells you how much grog was added to the clay. The measurement tells you the particle size of the grog.
Working with heavily grogged clay
After reading this you may be thinking “I’m picking clay with a lot of grog all the time!” But let me pass on some warnings. And I’ll break my warnings up into “building with grog” and “decorating with grog.”
Building with grog
Throwing with heavily grogged clay is a challenge. It’s harder to center because it’s heavier. And it’s rough on your hands. So expect some soreness the first few times throwing with heavy grog clay.
On the flip side, the more grog the better with handbuilding pottery. If you’re working on a piece that is larger or complex or needs structural strength, go with heavy grog clay over fine grog clay.
Decorating with grog
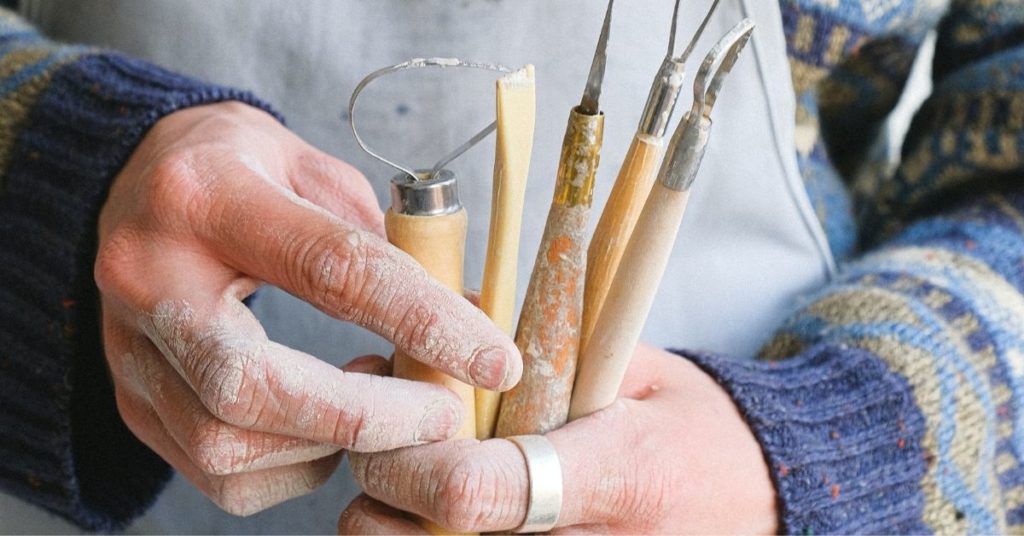
One of the biggest downsides of using clay bodies with a lot of grog is how it affects your finishing work. The larger particles in the clay can cause your tools to get stuck or veer off course if you’re carving or trying out sgraffito. Instead of a clear line, your piece will likely have a scratched look to it.
Alternatively, grog isn’t great if you’re making a piece that requires you to sponge the piece for moist clay. The sponge will pull the finer particles away from the clay body. The end result will be a bumpy surface texture. You can use a wet finger instead of a sponge.
Grog can also effect the color of the piece. So if you’ve specifically selected white clay or red clay for their beautiful finish, make sure you look up how your grog content can change the end outcome.
How much grog do you add to clay?
Like so much in ceramics: It depends. And the best answer I can give is to try different particle sizes in different pieces to see what works best for your pottery.
BUT I can give you some rules of thumb:
1. Smaller pots need less grog
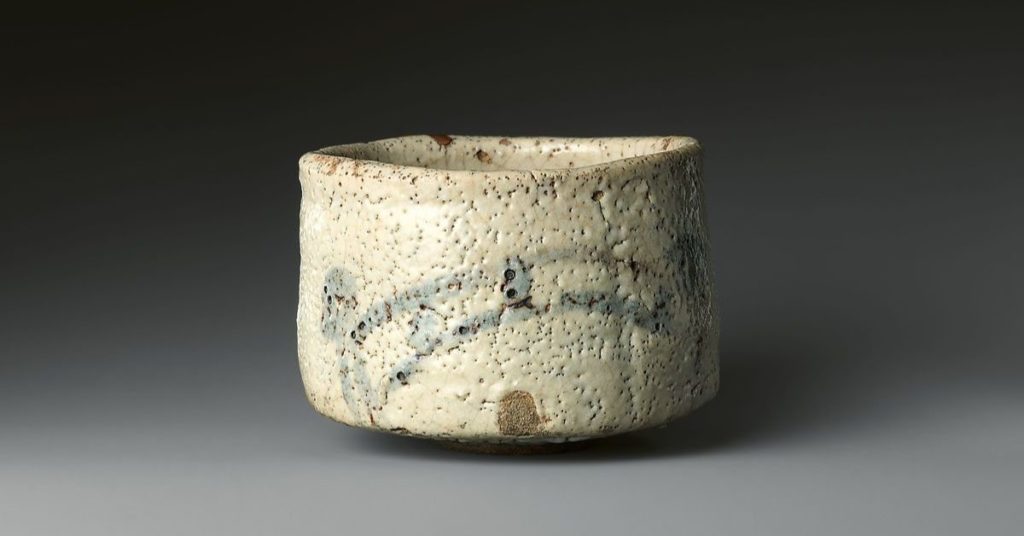
Again, this goes back to the structure grog provides with big pieces. So the smaller you make a pot, the less grog you’ll need to have it hold up from throwing to firing.
2. If you’re a beginner throwing on the wheel, use less grog
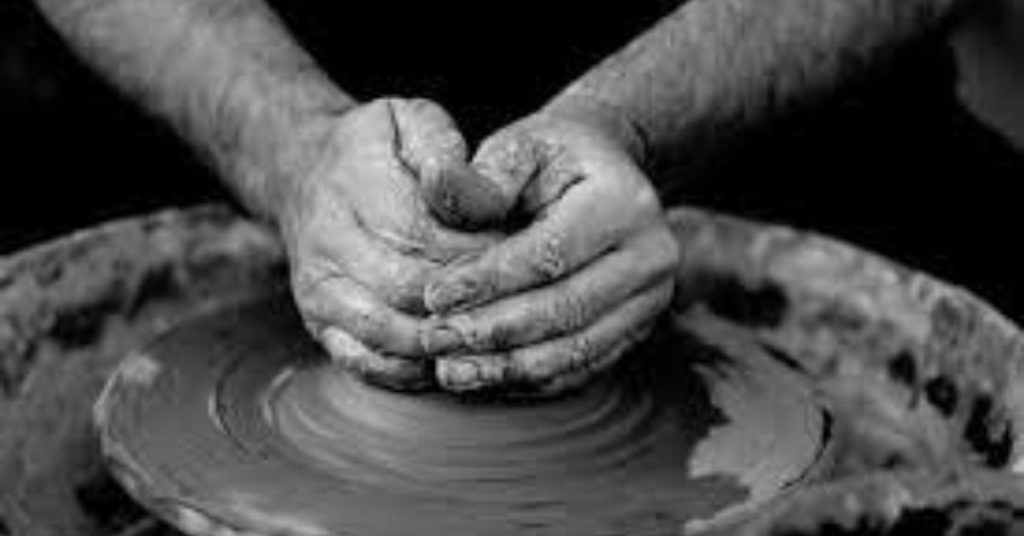
I suggest less grog or no grog at all for beginner potters. There are really two reasons for this.
First, the less grog that’s in the clay body, the less you have to fight the material. Low grog clay can give a new potter a more tactial experience when working with clay. With less grog, a potter is going to have an easier time centering on the wheel and building walls.
Second, grog can hurt! Think of it this way: Find your finest sandpaper and rub it on your arm for a few seconds. It might hurt a little bit, but you’ll be all right. Then find your coarsest sandpaper and rub it on your arm for a few seconds. Much different, right?
It’s the same with grog. The more grog content in the clay or larger-sized grog content, the more it hurts the potter’s hands.
3. More grog can help with handbuilding
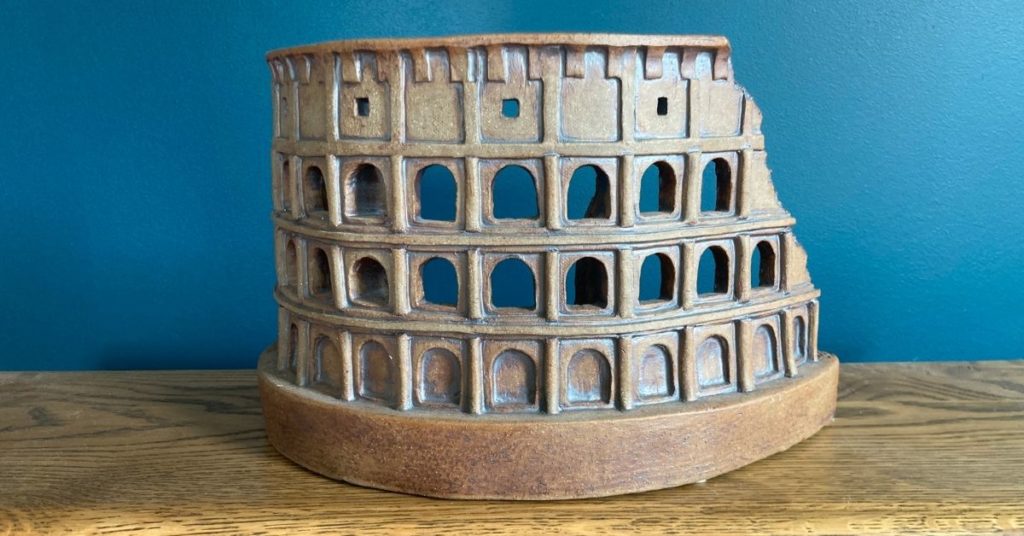
With hand building, I’m less concerned with the grog size UNLESS I’m making a big piece. If I’m making a big piece, I’ll need a clay with a higher grog content.
Conclusion
That’s it! You’ve learned EVERYTHING you need to know about grog (not really ;)).
Whether it’s preventing firing shrinkage or structurally supporting your pieces, grog is an important part of the pottery-making process. I hope learning about it today opened your eyes to how you can apply grog to your upcoming project.
If you have any questions, leave a comment or simply email us at hello@wheelandclay.com. We’d be happy to help.
Related Articles
6 causes of clay cracking in pottery
How to choose pottery clay for your next project