An Introduction to Crystalline Glazed Pottery
Crystalline glazed pottery is a unique form of ceramic art that showcases magnificent crystals in the finish. This style leverages a glaze matrix with coloring oxides like zinc oxide to create distinct crystal formations during the firing process. It’s all chemistry folks!
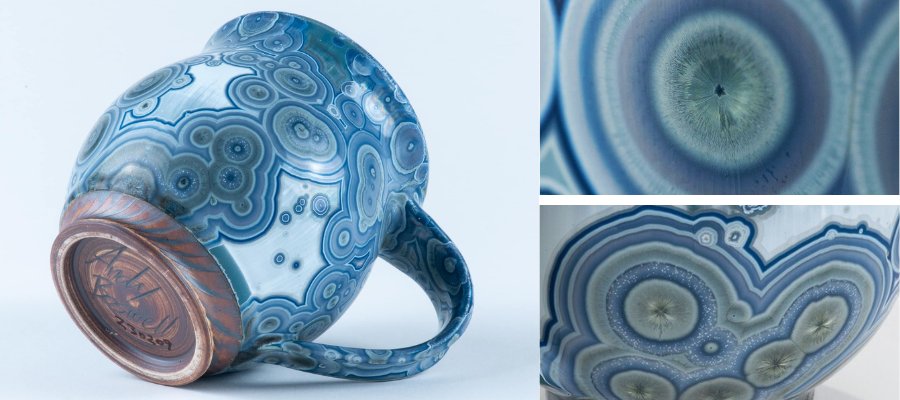
My goal here is not to provide a scientific breakdown of the actual chemical process, but zinc and silica are positively and negatively charged, resulting in covalent bond which becomes the nucleus of a crystal. Ok ok, sorry. The remaineder of this will be focusing on technique, some requirements and background.
With a gamut of finishes and glaze combinations, crystal glazes offer limitless possibilities for ceramic artists to experiment and create enchanting pottery pieces. Note that crystalline glazes are not usually recommended as dinnerware.
While some off-the-shelf glazes are nontoxic, the surface characteristics of the final piece may not be up to par. You could buy premade glazes that can fire at cone 5. Some brands offer good consistency and effect considering this low fire. To create crystalline pottery in the likes of Robert Hessler, Andy Boswell or Matt Horne, you’ll need custom recipes, a finely tuned process and patience!
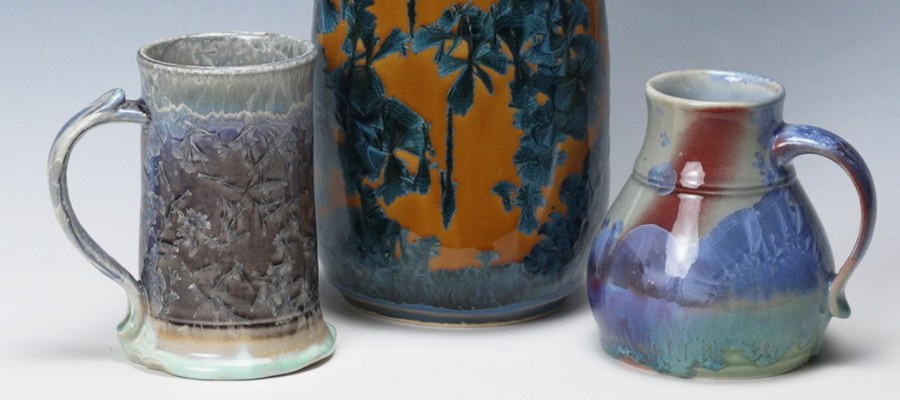
The firing schedule and kiln temperature play a crucial role in determining the final outcome, as the crystals require an extended period of time to develop their characteristic needle-like shapes or flower-like effects.
The molecular characteristics of the glaze, including the percentages of zinc and silica oxide molecules, along with the clay body, all contribute to the formation of the crystals. It can be difficult to grow two different colors of crystals in your laze, but we’ve seen experiments that led to this.
History of Crystal Glazed Pottery
Crystal Glazes Pottery has a history as fascinating as its finish. It is thought that it originated in ancient China. Since then, it has seen multiple advancements, with artists discovering new techniques and glaze recipes to elevate the beauty of the crystal finishes about 100 years ago.
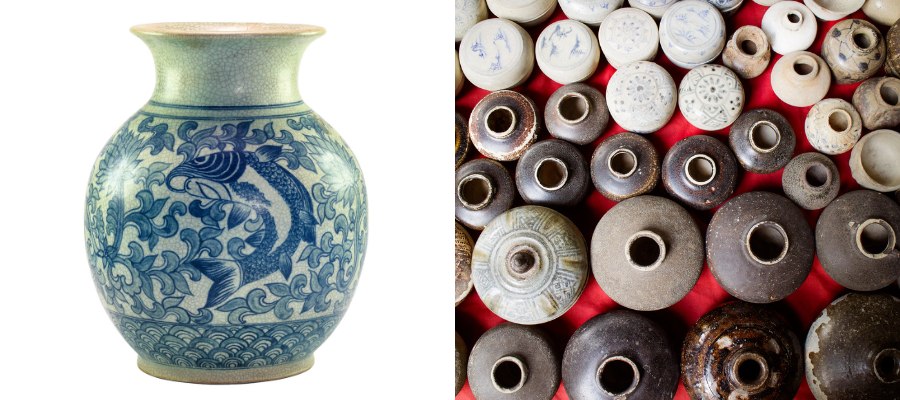
Today, crystal glazes continue to dazzle pottery enthusiasts with their unique, vibrant finishes and captivating crystal structures. Crystals on pottery were considered a defect way back!
The Role of Specialty Glazes
Crystal glazes are truly special when it comes to pottery. A crystalline glaze that imbues life into each piece should be freshly mixed and sieved for optimal crystal-growing potential. (Yes, the crystals are grown!)
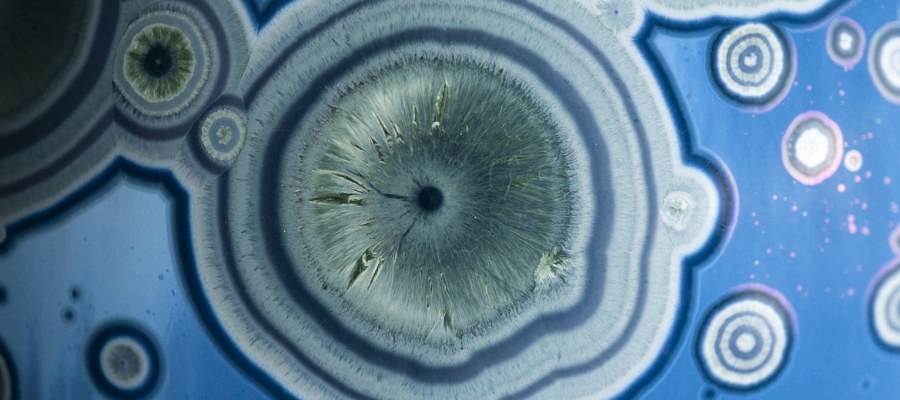
Certain colorants, including cobalt, nickel, copper, iron, and manganese, can migrate into the crystal structure. This adds additional depth to the piece. When done right, it can have stunning impact. Cobalt is known to be the strongest colorant.
Some potters prefer spray booths, but we’ve found dipping to be preferable for smaller pieces. I get an even spread and efficient application.
Crystalline Glaze & Application
There are a variety of tools and techniques used in crystal glazes pottery to achieve the desired effects and finishes. These can range from the type of clay body used to the method of glaze application and firing schedule. Temperature fluctuation when firing may reduce your success, so a controller is a ideal for holding. Cone pads are also great for ensuring your kiln is firing like you expect!
Clay Body
The type of clay body used can have a significant impact on the final outcome of the pottery piece. High-fired porcelain is often preferred for crystal glazes pottery due to its smooth surface and ability to withstand high firing temperatures.
Glaze Application
The way the glaze is applied can also impact the final result. Thicker applications of glaze can lead to larger crystal formations, while thinner applications result in smaller crystals. It’s also possible to layer different glazes to create unique color combinations and effects.
To Spray, Pour, Dip or Brush?
Well, it depends. If your piece is very large, you will not want to prepare a 15-gallon bucket of glaze to dip it in! In that case, you may want to pour the glaze over the peice. Crystalline glaze will flow, so you don’t generally need to worry uneven pouring. You can add total thickness by doing multiple pours and layers.
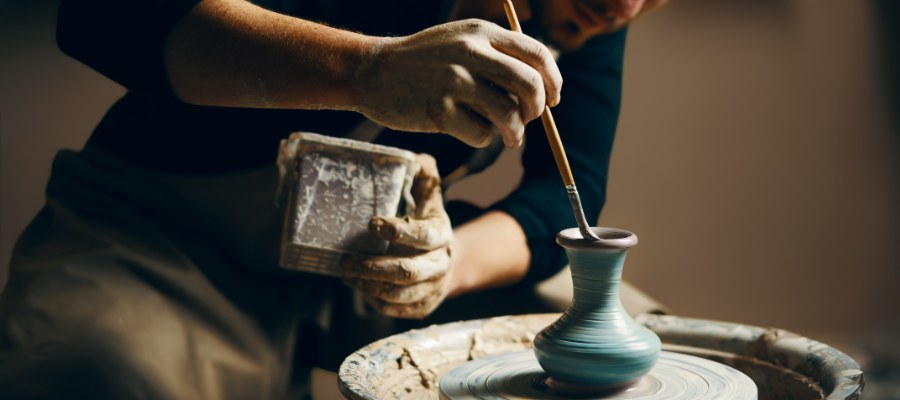
Some ready-to-use mixes state that a small fan brush should be used for application. So keep this in mind. Read the directions before use.
The Art of the Glaze
Crystal glazed pottery comes with numerous benefits for artists and pottery enthusiasts alike.
It’s capacity to create distinctive crystal growth within the fired glaze matrix, produce various sizes of macro-crystals, offer versatile finishes, and provide an extensive range of color options, makes it an artisan’s delight.
Each piece becomes a mesmerizing, one-of-a-kind artwork. Search Etsy or Pinterest to see some stunning examples and what prices some of these high-quality pieces fetch.
Crystal Glaze Recipes Vs Ready-Made
Being a chemist can serve you well if you would like to formulate your own glaze recipes. For the rest of us, a pre-made recipe is likely the best approach!
If you are interested in a challenge and opportunity to create something truly unique, consider visiting https://glazy.org. They provide a massive amount of community info on glazes and ceramics.
Below is a sample recipe from one of my favorites, Louis Katz. You’ll see what I mean when I say ‘chemistry’ and art!
- Cone: 10
- Firing: Ox. or Red.
- Recipe: Percent Batch
Comments:
1.05% RIO – white crystals on a pale yellow background
1.05% Copper Carbonate – green crystals on a pale green background
1.22% Manganese Dioxide – mauve/pink crystals on a mauve background
0.23% Cobalt Carbonate
0.70% Manganese Dioxide – blue crystals on a gray background
2.62% Green Iron Oxide
2.62% RIO – royal blue crystals on an orange to red/brown background
1.22% Manganese Dioxide – pink crystals on a mauve background
These glazes can be fired on over the other!
Firing Crystalline Glazed Pottery
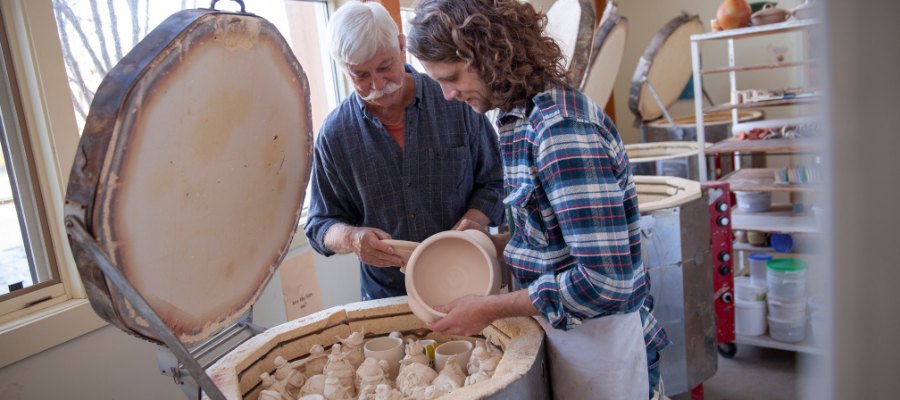
The crystals in your glaze will form during the firing phase. Knowing what crystals you will get at what specific temperature is very helpful. Using a cone will also allow you to better understand when the glaze is molten and flowing.
After the initial crystal growth, you have the option to alter the crystal’s color and the number of rings it exhibits by subjecting it to different temperatures in the kiln. This usually involves holding it at higher and lower temps, so a modern kiln with a digital controller is best. You will struggle using an older kiln and with a kiln sitter.
The atmosphere within the kiln can also influence the formation of crystals. Reduction or oxidation atmospheres can impact the color and shape of the crystals, adding another layer of complexity to the process. In a manual kiln, growing rings can be difficult, but you can develop some crystal growth.
Temperature Accuracy
Crystalline glaze firing requires an understanding of ceramic materials, glaze chemistry, kiln operation and accurate temperature measurement. Did I mention your kiln must be able to easily reach cone 10 for most recipes?
An accurate temperature controller is also a must. Ultimately, slow firing and precise temperature control are crucial for achieving optimal crystal growth. Using thinner shelves can reduce the negative impact of heat-dampening effects.
Companies such as L & L Kilns create cone 12 kilns specifically for crystalline glaze firing. They start at roughly $6,500. Not your entry level option, or if you are still wondering what the cost of starting pottery might be!
A specific firing schedule is required to grow the crystals, making this a technically challenging process. This is for advanced potters who have the proper equipment on hand. High temperature combined with longer firing time means crystals have time to grow.
All of these details and requirements culminate in crystalline glazed pottery fetching higher prices than your clear glazed pinch pot.
Glaze Overflow & Protecting Kiln Shelves
Crystalline glaze is usually runny, so overflow is common.
Protecting your kiln shelves is a must. You can take preventative measures, such as using a catcher or collection dish. Having a good kiln wash on-hand is also important.
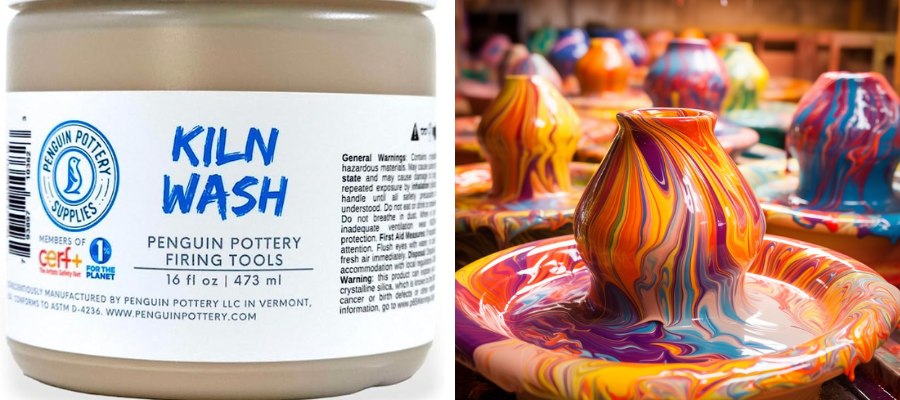
Some people refer to kiln wash as “shelf primer”, since it’s basically a protective coating applied to shelving or furniture inside the kiln.
If you need to apply this, make sure the shelves start off clean. Then use only a thin, even layer for max protection. This barrier will prevent any of the glaze from fusing to surfaces in the kiln
A glaze catcher is a cup shaped ring that usually is glued to the piece. A collection dish will add more work and cleanup to the piece. I’ve also rarely seen them reused.
Is Crystalline Glazed Pottery Food Safe?
No one likes this answer, but: it depends.
Some potters improve the functionality of their pieces by developing specific processes and glaze recipes.
Andy Boswell from Boswell Studios, for instance, discussed how an acid dip can be used to etch metals that might otherwise leach from the glaze. Furthermore, avoiding crazing helps prevent food from easily penetrating the pottery’s surface.
Consider using a liner glaze that is not crystalline if food safety is a concern.
Next Steps
If you’re ready to jump into the world of crystal glaze, you can start by getting a premixed glaze, or continuing to learn about glaze recipes and firing techniques.
I hope this introduction was enough to pique your interest and start your journey on creating some incredible pieces. Please feel free to share them with us and we’ll post them on our Facebook page.
Joanna Miller
Clay Maven
I’m an artist and educator who’s head over heels in love with pottery and ceramics. Seriously, I’ve got clay running through my veins! From the moment I first touched that squishy, magical substance as a kid, I knew I had found my calling. Now I help others, from hobbyists to professionals, become their best self.
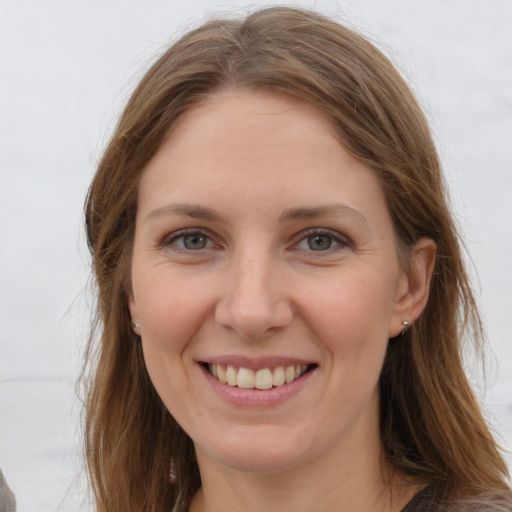